Understanding the Essentials and Applications of Plastic Extrusion in Modern Manufacturing
In the realm of contemporary manufacturing, the method of plastic extrusion plays an important function. Deciphering the basics of this process exposes the true flexibility and potential of plastic extrusion.
The Basics of Plastic Extrusion Process
While it might show up complex, the fundamentals of the plastic extrusion process are based on fairly straightforward principles. It is a production procedure wherein plastic is thawed and afterwards formed into a constant profile with a die. The raw plastic material, usually in the form of pellets, is fed into an extruder. Inside the extruder, the plastic goes through warmth and stress, creating it to thaw. The molten plastic is then forced through a designed opening, understood as a die, to develop a long, continual product. The extruded item is cooled down and after that cut to the wanted size. The plastic extrusion procedure is thoroughly used in different markets due to its flexibility, cost-effectiveness, and performance.
Different Kinds Of Plastic Extrusion Strategies
Building upon the fundamental understanding of the plastic extrusion process, it is required to explore the numerous techniques entailed in this production technique. In contrast, sheet extrusion develops big, flat sheets of plastic, which are generally more processed right into items such as food product packaging, shower curtains, and auto components. Understanding these techniques is key to using plastic extrusion successfully in modern manufacturing.
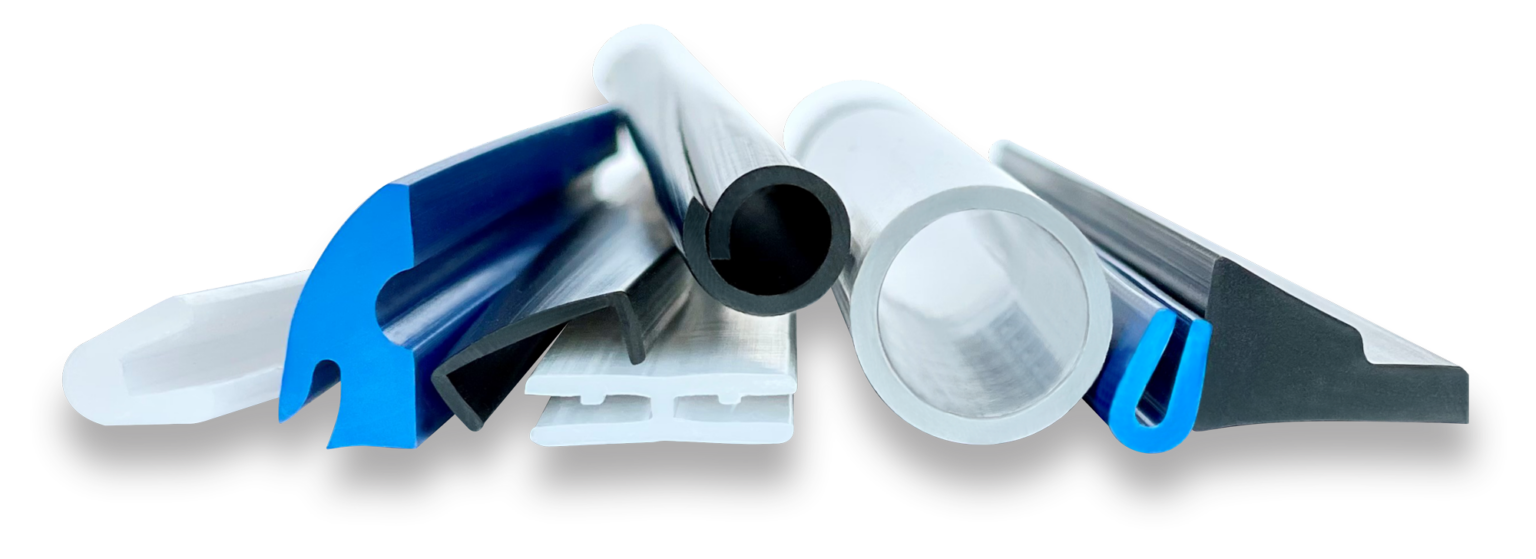
The Role of Plastic Extrusion in the Automotive Industry
A frustrating majority of parts in modern-day vehicles are items of the plastic extrusion procedure. This procedure has transformed the vehicle sector, transforming it into an extra efficient, economical, and flexible production sector. Plastic extrusion is mainly made use of in the manufacturing of different car elements such as bumpers, grills, door panels, and control panel trim. The process offers an attire, constant outcome, making it possible for manufacturers to produce high-volume get rid of fantastic precision and minimal waste. The agility of the extruded plastic parts adds to the general decrease in Find Out More car weight, improving fuel effectiveness. The resilience and resistance of these parts to heat, cool, and influence enhance the long life of autos. Hence, plastic extrusion plays an essential function in vehicle manufacturing.
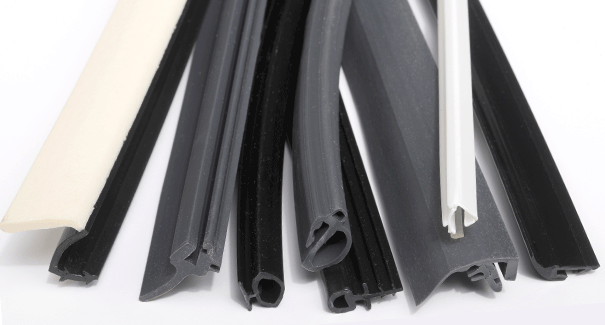
Applications of Plastic Extrusion in Durable Goods Manufacturing
Past its additional reading considerable effect on the automotive market, plastic extrusion proves similarly reliable in the world of consumer goods making. This process is essential in developing a broad variety of items, from food product packaging to home devices, playthings, and also medical devices. The convenience of plastic extrusion allows manufacturers to make and create complicated shapes and dimensions with high accuracy and performance. In addition, as a result of the recyclability of several plastics, squeezed out components can be recycled, lowering waste and expense. The adaptability, flexibility, and click here to read cost-effectiveness of plastic extrusion make it a favored choice for many customer goods suppliers, adding substantially to the industry's growth and innovation. Nevertheless, the environmental effects of this widespread usage require mindful consideration, a topic to be reviewed additionally in the succeeding section.
Ecological Influence and Sustainability in Plastic Extrusion
The pervasive use of plastic extrusion in making invites scrutiny of its eco-friendly ramifications. Efficient machinery lowers power use, while waste management systems reuse scrap plastic, lowering raw product demands. Despite these renovations, even more innovation is required to reduce the ecological impact of plastic extrusion.
Conclusion
In verdict, plastic extrusion plays an important duty in modern manufacturing, specifically in the automobile and consumer products industries. Comprehending the fundamentals of this process is crucial to optimizing its benefits and applications.

The plastic extrusion procedure is thoroughly utilized in different industries due to its performance, flexibility, and cost-effectiveness.
Building upon the basic understanding of the plastic extrusion procedure, it is needed to check out the various strategies included in this manufacturing method. plastic extrusion. In comparison, sheet extrusion creates huge, level sheets of plastic, which are usually further refined into products such as food packaging, shower curtains, and car parts.A frustrating majority of components in modern vehicles are products of the plastic extrusion procedure